We are asked by customers on a regular basis to come up with solutions for Engineering problems and 99% of the time our team come up with the answers. With the help of decades of experience from our engineers and the latest design technology even the weird and wonderfull have been acheived.
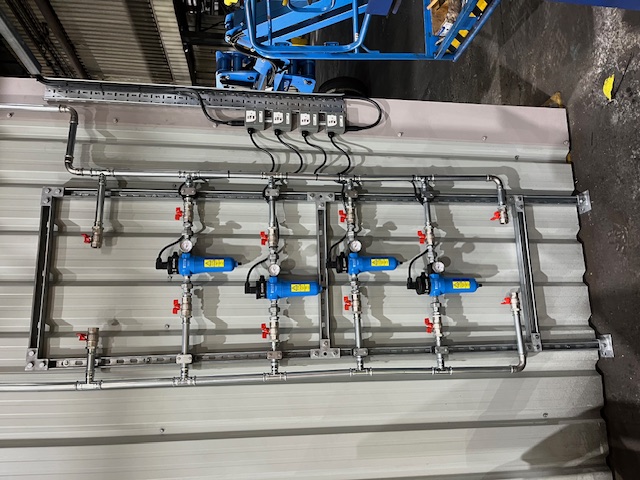
Case Study 1 –
Problem – Pneumatic tool wear and operator health concerns.
In a steel works the use of pneumatic hand air tools for fettling and grinding is a common practise. Along with regular breaks and controls for health and welfare of the operators the issues are out fo the control of the customer. The constant use of the air grinders means wear of the tools and the freezing of clutch and gears can mean tool life is reduced drastically. Add to this the cold from the tool to the operators hands can make it uncomfortable on long daily use.
Solution – A manifold was created to with family of four Walker Air Heaters in line. The temperature is raised to maintain a constant warm flow of air to the tools in the fettling bay. This has improved the tool life and the operators ease of use considerably.
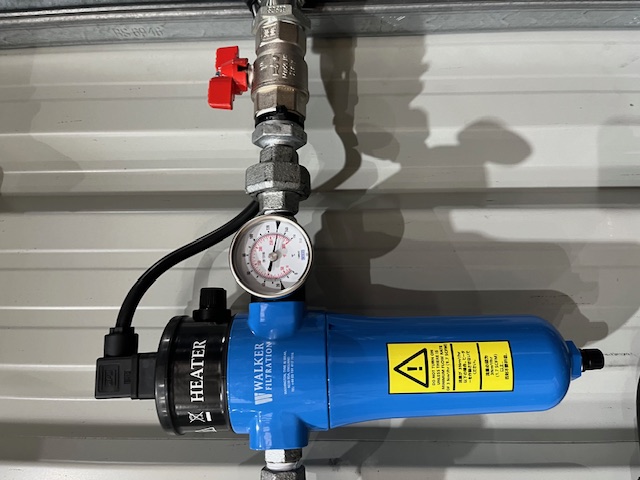
Case Study 2 –
Problem – Repeat Failure on Warm Air blower
A customer had an old warm air heater from the 1950’s that was constantly having issues with failing heater elements which were becoming rarer than hens teeth to get hold of. The warm air was for an old amenities block in steel works which was very restricted on space due to some areas of the building being unsafe with asbestos and access issues. We came up with a plan to to fit a warm air blower that we would retrofit into a storage area and couple up to the existing warm air ducting which incredibly fed the shower blocks, toilets and with some old school engineering was also fed into the personel lockers to dry wet clothes and towels.
Solution –
New gas pipes and bespoke fabricated ducting installed in record time and with little intrusion to the running of the amenitity block. Towels and wet clothes kept drying to keep the staff happy.
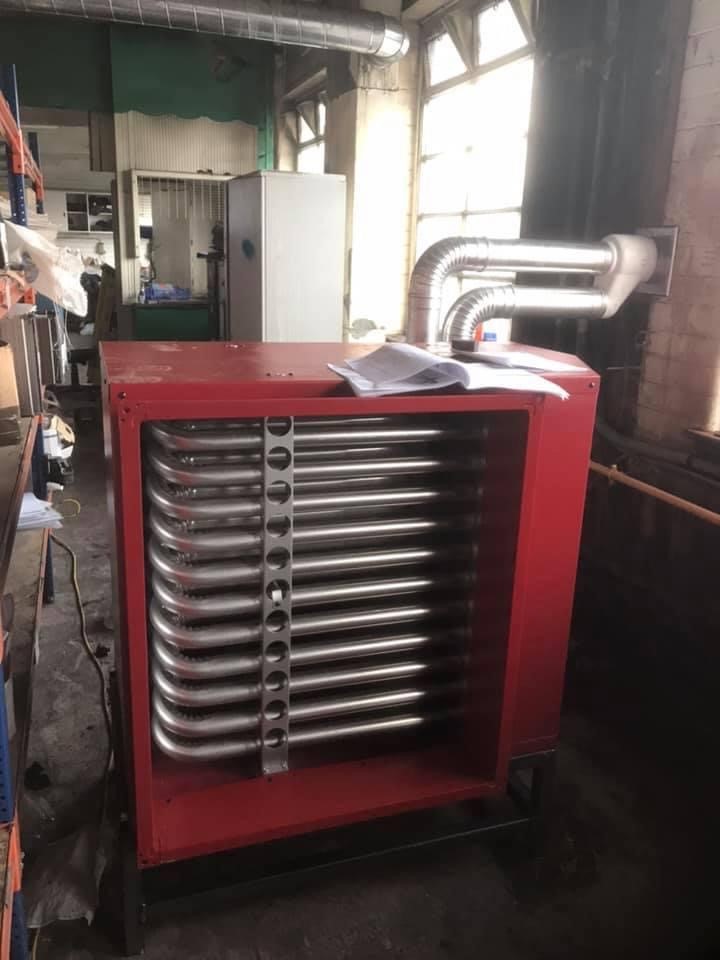
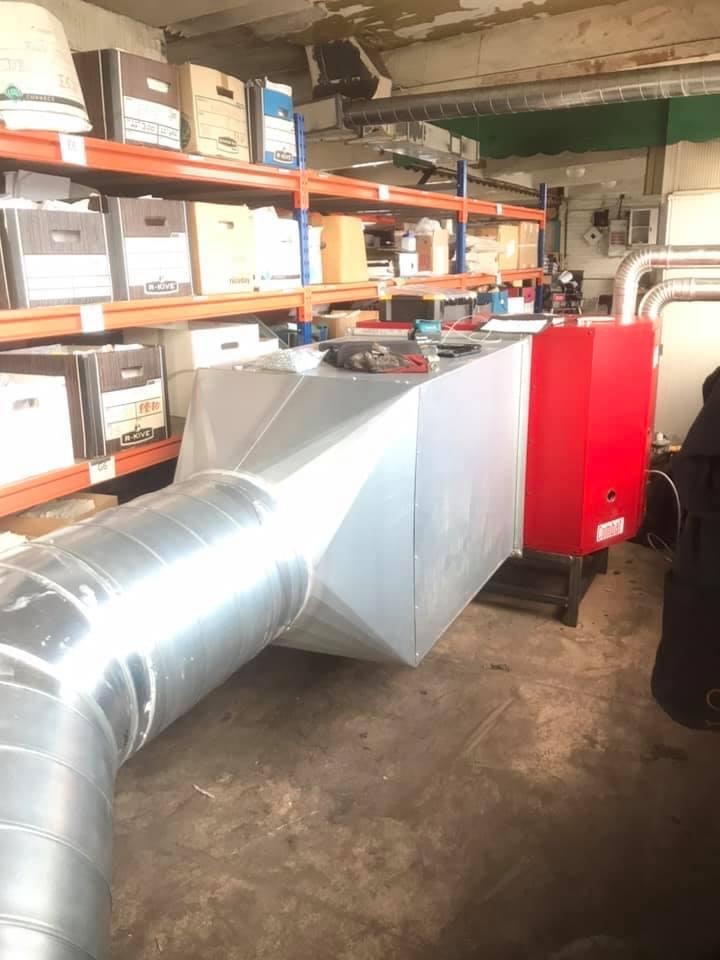
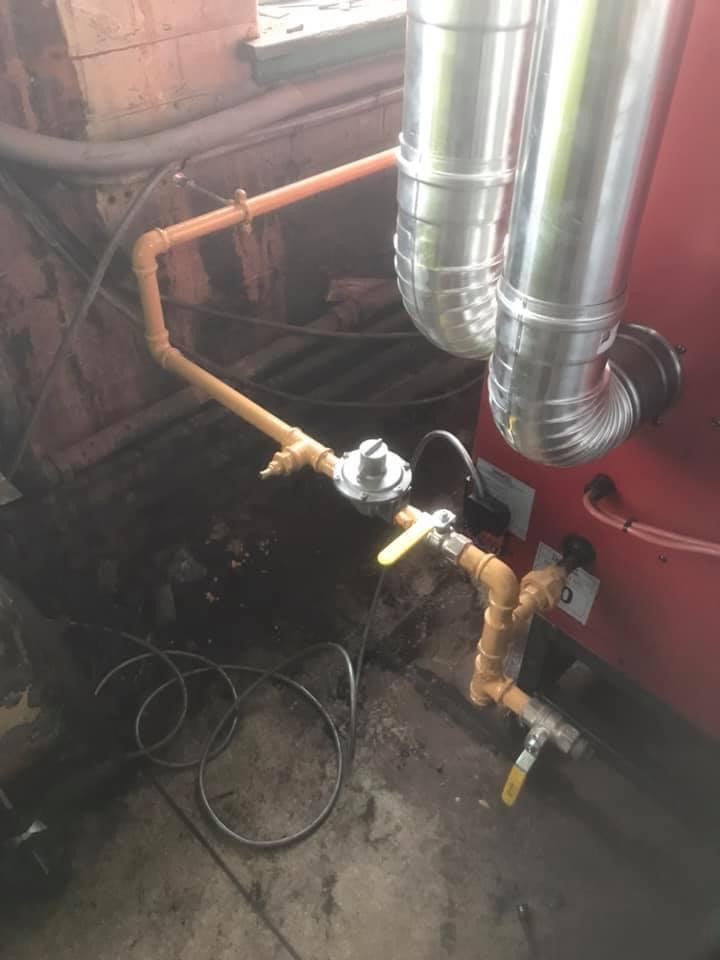